This website uses cookies so that we can provide you with the best user experience possible. Cookie information is stored in your browser and performs functions such as recognising you when you return to our website and helping our team to understand which sections of the website you find most interesting and useful.
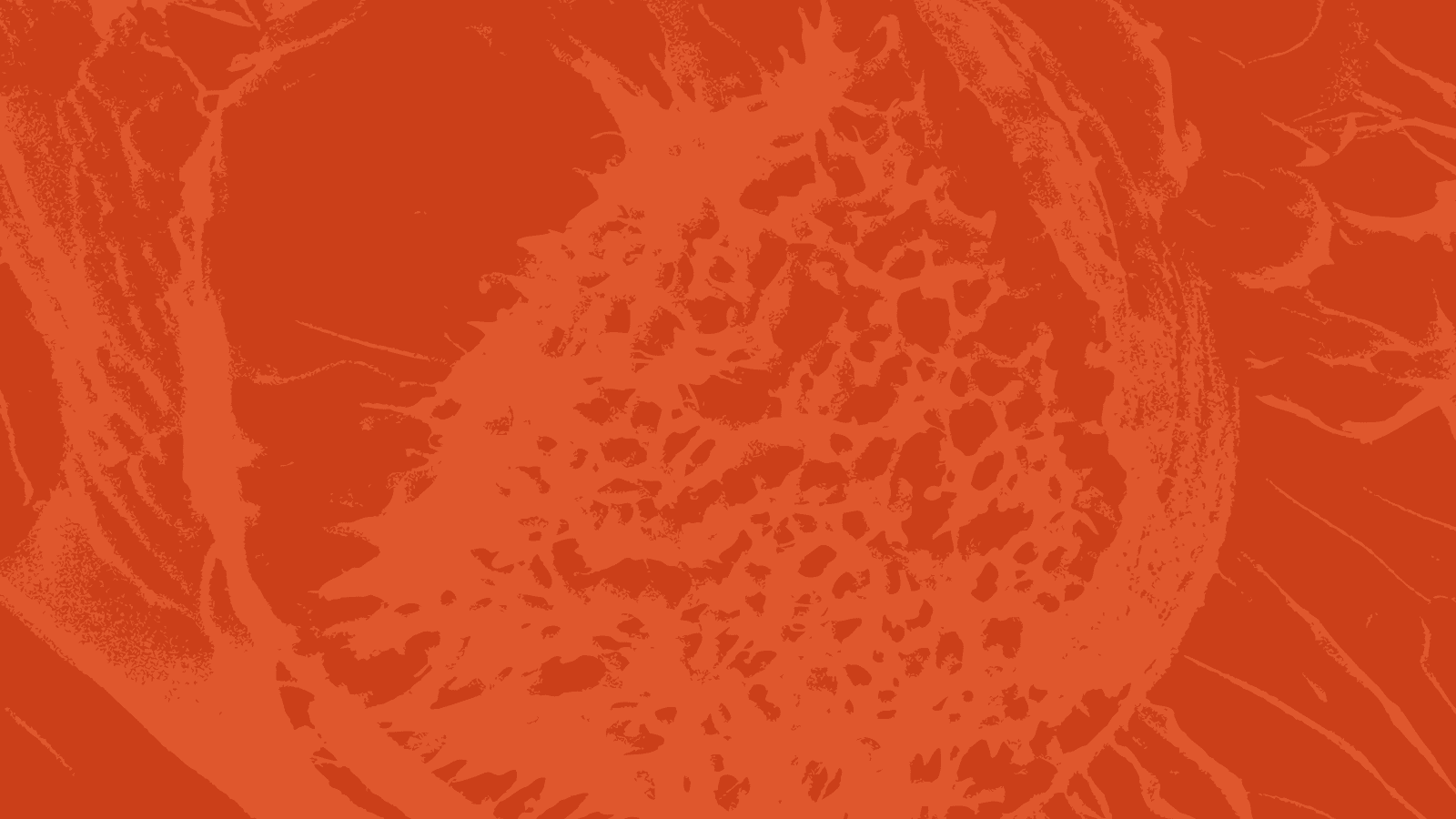
Automated Formulation of Materials
Technology Platform
HT Formulation and Measurement capability
The Materials Innovation Factory (MIF) has a suite of robotic platforms suitable for automated formulation, and working at a range of scales suitable for materials discovery and product development.
To further advance the MIF capabilities, Royce has invested ~£3M in developing the Formulation Engine (FE) in partnership with Labman Automation, a UK SME focussing on bespoke laboratory automation platforms. The FE is a large modular robotic system that will provide academic and commercial scientists with the tools to increase their scientific outputs quickly and efficiently in a controlled environment.
The FE is designed to be as future-proof as possible and wholly expandable for future research challenges while retaining the benefits of static automation platforms such as high throughput and reliability. With its modular design, it allows up to eight separate independent automated modules to be docked into the main robot platform simultaneously for high throughput and interlinked workflows such as make and measure. Input vials ranging from 2–200ml are easily handled by the FE’s two FANUC arms which deliver materials and consumables to the modules as required so that several workflows can happen independently whilst sharing the robots’ resources.
The Main Platform consists of four areas: the consumables zone which can handle various consumable types from 2ml HPLC vials up to 200ml plastic pots, the materials library, the transport system, and the module bays. Formulations are made in consumables (pots, vials and SBS format plates), which are loaded into the consumable zone (via a human operator). The materials library contains Mobile Dispensing Units (MDUs) which are filled with raw ingredients (via a human operator) for formulating and are controlled by the Main Platform PC over Wi-Fi. The transport system consists of two FANUC robot arms which transport the consumables and MDUs from their racks to the docked processing modules in the eight module bays.
Module Bays
Dispensing module (DMOD): module dispenses into various consumables fed from the main platform. It dispenses powders into boats in a dehumidified atmosphere. It also contains four fixed syringe needles for low viscosity additions.
Inert processing module (XYZ): gantry robot for moving consumable and performing syringe needle transfers across various consumables from 2ml HPLC vials up to 40ml glass vials. It also houses a Mettler Toledo Quantos for highly accurate powder dispensing. Syringe pumps dispense up to six stock solvents and allow gas caps under nitrogen or a It can cap, crimp, shake and ultrasonicate vials.
Fluid processing module (TOM): providing three independent mixing stages with excellent distributive and dispersive mixing for process-sensitive materials at 50ml or 200ml scale. Gravimetric additions can be made whilst mixing, homogenising and controlling temperature. pH can also be measured and adjusted.
Photocatalysis module (PCAT): completes the photocatalysis workflow for materials discovery and research. Following the XYZ processing module, new catalysts are exposed to light from a solar simulator to promote water splitting and carbon capture. The headspace of each sample is analysed using a mass spectrometer to detect if the reactions were successful.
Platform Lead
Dr Michael Egan, IET, CMI
Technology Platform Lead: Automated Formulation of Materials
Dr Michael Egan is a chartered Engineer (IET) and Chartered Manager (CMI) and joined the Materials Innovation Factory team at the University of Liverpool in June 2015 as a senior member of the technical team focussing on automation, robotics and formulation.
He graduated with a PhD from the University of Liverpool’s Department of Engineering in 2007 in the field of industrial design and management, specifically developing new equipment for 3D printing. He then moved to Chemistry to manage the operation of the Ultra Mixing and Processing Facility (UMPF), developing new fluid processing technologies for commercial exploitation, and including process scale up and installation of pilot plant machines in two commercial sites.
For the past seven years, he has been driving development of the Material Innovation Factory’s automation capabilities, including development of a £3M automated robotic platform for material chemistry called the Formulation Engine.
In 2022 he was appointed as Technology Platform Lead for the automated formulation of materials at Royce with the aim of supporting the commercial/academic exploitation of the MIF’s automated capabilities.