This website uses cookies so that we can provide you with the best user experience possible. Cookie information is stored in your browser and performs functions such as recognising you when you return to our website and helping our team to understand which sections of the website you find most interesting and useful.
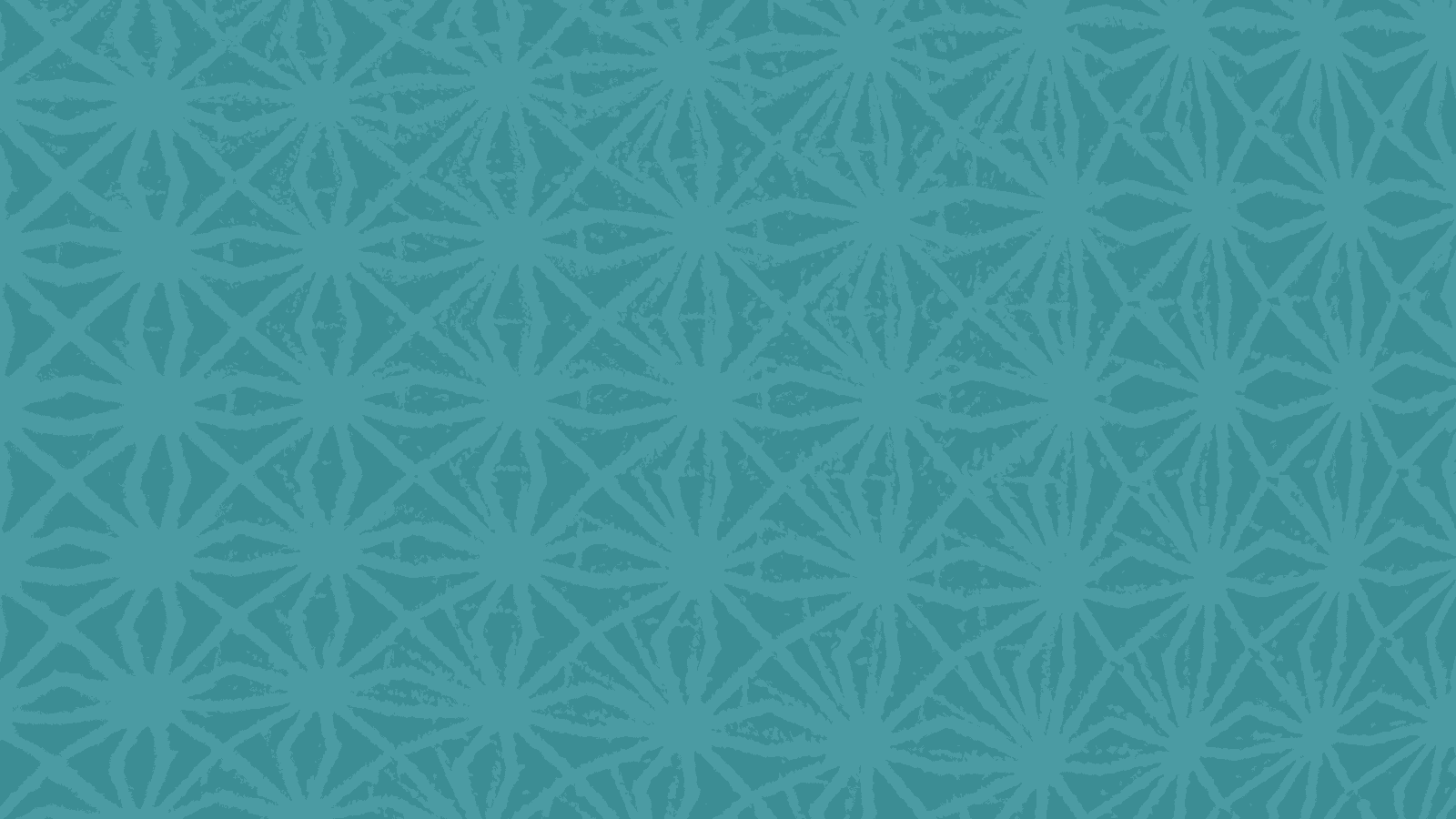
Advanced Characterisation To Understand Radiation Damage in Materials
Technology Platform
About
The Advanced Characterisation to Understand Radiation Damage in Materials Technology Platform brings together the extensive novel characterisation facilities offered across the Royce institutes with state-of-the art active materials development, in order to investigate radiation damage in active and non-active inorganic materials. The objective of this technology platform is to facilitate development of materials for the next generation of fission and fusion power stations, and realise the Royce ambition to develop vibrant industry- and academic-led programmes which accelerate nuclear’s contribution to decarbonisation.
Radiation damage in materials for nuclear power can take on many forms. Neutron irradiation can displace atoms in a material leading to changes in crystal-, micro-, and nano-structures, as well as result in transmutation leading to a change in material composition and the production of the transmutation gases, helium, and hydrogen. For alpha-emitting waste materials, the alpha-daughter recoil nuclei induce high levels of atomic displacements and the alpha-particle can induce chemical changes by ionisation and excitation processes in materials before eventually transforming into helium. The surface of plasma-facing materials for fusion can change due to plasma-surface interactions, resulting in surface nano-structuring, erosion, and tritium retention. This technology platform enables examination of all of these radiation induced damage effects.
To develop materials for the next generation of fission and fusion power stations, characterisation of radiation damage in non-active materials is often first undertaken in order for a wide range of materials to be surveyed without the need for active handling capabilities. Energetic ion implantation is a method commonly used to induce atomic displacements and gas production analogous to neutron- and alpha-irradiation, without generally rendering the material radioactive. However, ion implantation often only damages the surface of materials, up to about a micron. Within Royce, we have the capabilities to probe only this damaged surface region. For example, to determine any implantation induced changes to crystal structure (including structural units in amorphous materials such as nuclear waste glass analogues) we offer X-ray diffraction (XRD) in grazing incidence and UV Raman spectroscopy. We can utilise transmission electron microscopy, including atomic-scale resolution capabilities, and electron probe microanalysis (EPMA) for the characterisation of implantation-induced defects, including secondary phase and gas bubble formation and elemental segregation, and offer site specific plan-view and cross-sectional sample preparation.
The next stage in nuclear materials development is in producing and characterising active materials. This technology platform includes state-of-the-art equipment and instrumentation for materials formulation, processing, characterisation, and performance assessment of active materials comprising α and β, γ nuclides, including solid-state plutonium. Processing of these active materials can be carried out via conventional solid state synthesis using our suite of high temperature furnaces, or by using the UK’s only radiological Hot Isostatic Press operating up to 2000 ℃ and 200 MPa. This technology platform houses extensive active material characterisation facilities, including diffraction and spectroscopy (e.g., XRD, Raman, X-ray absorption and emission spectroscopy), microscopy and microanalysis (e.g., atomic force microscopy, optical profilometry, and EPMA), Thermal and physicochemical analysis and Chemical and radiochemical analysis.
Platform Lead
Dr Amy Gandy
Technology Platform Lead: Advanced Characterisation To Understand Radiation Damage in Materials
Amy Gandy is Senior Lecturer in Nuclear Materials Engineering, and previously held a Royal Academy of Engineering / Leverhulme Trust Research Fellowship in Understanding Radiation Damage Mechanisms in Novel, Compositionally Complex Alloys. Amy completed a joint PhD at the University of Salford and the University of Poitiers, France, in 2009 for which she used transmission electron microscopy (TEM) to understand ion beam implantation induced defect formation and interactions during thermal annealing in crystalline and amorphous silicon, relevant to the semiconductor industry. Between 2009 and 2015, Amy undertook postdoctoral research positions at the Universities of Manchester and Sheffield investigating radiation damage in inorganic materials, with a focus on nuclear materials from 2011. Her current research focuses on new materials development for fusion, and radiation-induced damage and recovery mechanisms, and gas bubble formation, in poly-crystalline oxide-based materials and compositionally complex alloys for both fission and fusion, in collaboration with the UK Atomic Energy Authority (UKAEA), National Nuclear Laboratory (NNL) and Atkins Global.
Equipment
Multipurpose field emission transmission electron microscope with high spatial resolution and improved analytical performance.
The F200 is capable of high sensitivity and resolution materials analysis.
The JEOL JEM-F200 is a 200kV S/TEM equipped with a Cold Field Emission Gun for high brightness and a narrow energy spread, supporting high energy resolution electron energy loss spectroscopy (EELS). Dual Silicon Drift Detectors (SDD) enable high sensitivity and throughput X-ray analysis.
The F200 features:
- A quad lens condenser system to independently control intensity and convergence angle
- The SpecPorter automated sample holder transfer system
- A PicoStage to carry out precise sample movements
- A GATAN OneView camera to provide 16 megapixel imaging and video capabilities for TEM.
Field emission electron probe micro-analyser (EPMA) with enhanced imaging performance capable of quantitative elemental analysis (Be to U) from regions of interest down to 0.1μm.
This equipment is used for high accuracy chemical analysis and elemental mapping of a wide range of solid state materials such as defects, segregation, and identification of trace elements in: conventional and development alloys and ceramics, nuclear glasses, geological materials, archaeological artefacts, and a whole host of potential industrial applications.
The JEOL JXA-8530F Plus Hyper Probe, is a state of the art Electron Probe Micro-analyser (EPMA) capable of performing quantitative elemental analysis of small volumes (down to 0.1μm) in solid materials.
The instrument features an In-Lens Schottky Plus Field Emission Gun (FEG) electron source optimised to provide smaller analytical probe diameters at large probe currents, of the order of micro amps, enhancing the available imaging conditions over a wide range of analytical conditions.
The FEG source provides improved secondary electron imaging resolutions: 3nm at 30 kV to 50nm at 10 kV. It is therefore especially suited to performing analysis at lower kV, enabling sub-micron analytical spatial resolution of fine grained features.
The instrument is equipment with 4 X-Ray spectrometers (WDS), three 2 crystal configurations, and one equipped with 4 crystals, providing an analytical range from Be to U.
In addition, the instrument is fitted with a soft X-ray spectrometer (SXES) offering the possibility to study chemical bonding states in light elements.
The JXA-8530F Plus also comes with JEOL's 30mm2 silicon-drift detector (SDD). A high count-rate SDD along with an in-situ variable aperture enables EDS analysis at WDS conditions allowing survey analysis particularly useful for unknown samples.
EDS spectra, maps, and line scans, can be acquired simultaneously with WDS data.
Equipped with a Panchromatic Cathodluminescene (CL) system to enable high speed assessment of minute concentration differences particularly useful for the examination of minerals and mineral-like samples.
New multi-functional hard radiation XRD system allowing the study of advanced materials under in-service and extreme conditions.
The use of hard radiations enables:
- Total scattering studies of local atomic environments in both amorphous or crystalline materials
- High pressure studies using a diamond anvil cell
- Operando diffraction studies of coin or pouch cell type battery devices, so that electrochemical processes and changes in the crystal structure of an electrode material can be followed while e.g. a battery is being (dis)charged.
With its sample stage for big, bulky samples, the Empyrean is also the go-to machine for samples that are heavy (up to 5kg) or irregularly shaped. The Empyrean has a host of other applications under development also, so watch this space for more information.
A unique aspect of this equipment is the provision of access to high energy X-rays (Ag – 22keV) which will prove transformative in bringing synchrotron X-ray scattering techniques within reach of the laboratory. With its pre-aligned Fast Interchangeable X-ray modules for optics and stages, the diffractometer can be reconfigured simply and rapidly, allowing us to switch between different applications in a matter of minutes.
The PANalytical X’Pert3 is the go-to instrument for high resolution, high accuracy XRD, running in either standard, high temperature, or grazing incidence mode. The X’Pert3 uses the same sample changer system as the Empyrean, allowing it to run up to 45 samples autonomously.
The X’PERT is used for:
- Grazing incidence XRD (GIXRD)
- X-ray reflectometry (XRR)
- Texture and stress analysis
- High throughput powder and small solid diffraction
The instrument details are:
- Cu X-ray source (1.544A)
- Ni Kbeta filter
- Programmable divergence and acceptance slit
- Goebel mirror
- PIXcel1D detector
- 0.27 parallel plate collimator with secondary beam monochromator
- 45 position sample changer