This website uses cookies so that we can provide you with the best user experience possible. Cookie information is stored in your browser and performs functions such as recognising you when you return to our website and helping our team to understand which sections of the website you find most interesting and useful.
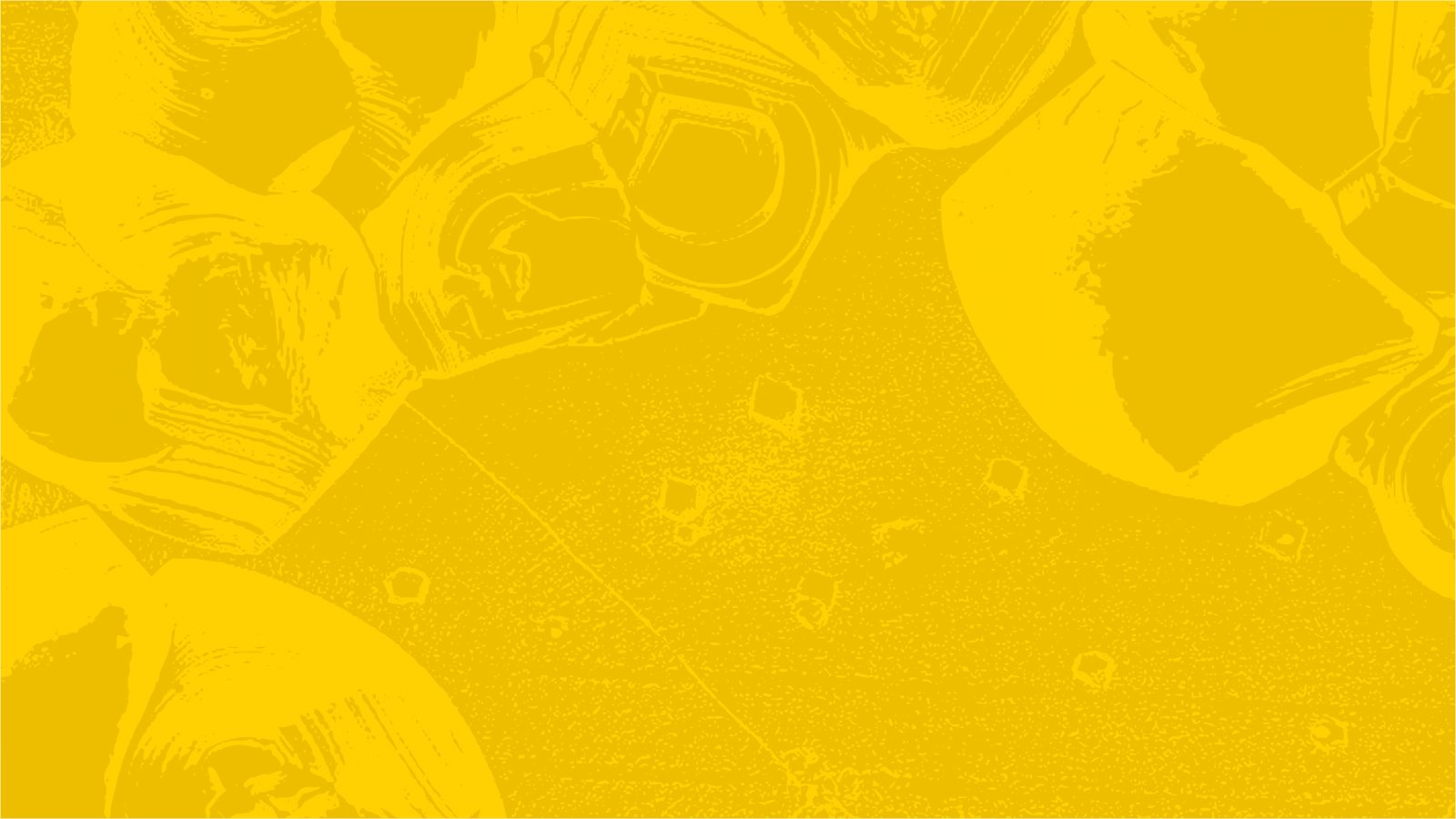
Ultimate Erosion-resistant Solutions for Wind Turbines
Royce’s Materials Challenge Accelerator Programme (MCAP) awarded £71K towards this project, which focused on edge erosion within the context of wind turbines. Edge erosion is a leading concern in wind turbines and represents a major fraction of the maintenance cost. This report presents the efforts to advance protective coating deposited directly on composites. The results demonstrate that the deposition of nanostructured nickel is a promising approach to avoid erosion.
Lightning strike and edge erosion of blades can represent up to 40% of the maintenance costs in offshore wind farms. Currently, composite solutions such as shells, tapes, and coatings are available to repair erosion. Metallic tiles provide the best protection, but they use harmful cobalt and are difficult to install. Our project explored an innovative solution that coat carbon fibres composites with a nanostructure layer of nickel.
Researchers from performed a Finite Element Modelling analysis (Figure 1) to estimate the required thickness of a nickel coating, such that no damage is transferred to the underlying composite. The results (Figure 2) suggest that tens to hundreds of microns should prevent damage.
Carbon fibre composites (Figure 3) were prepared and SIFCO brush plating was used for nickel deposition (Figure 4). Four different thicknesses of nickel were deposited, and their microstructural characterisation showed nanostructured grains ranging between 11 to 16 nanometres in size.
Erosion test showed dissimilar results. Samples with the thinnest coatings had limited erosion resistance. On the contrary, the thickest coatings resisted better the erosion and are good candidates to improve erosion resistance.
We continue to work in alloyed coating and functionally graded coatings enhance their adhesion. We are also exploring the use of this technology in turbine and tidal blades where maintenance is a challenge.
We have demonstrated for the first time the potential of electrodeposition techniques on carbon fibres. Our work has lay the path for the implementation of erosion-resistant solution for composites.
Prof. Andrew Starr
Head of Centre for Life Cycle Engineering and Management, Cranfield University
Collaborators
A multiskilled team with a range of expertise were brought together to contribute to this project across Cranfield University, University of Strathclyde and Sifco Ltd.