This website uses cookies so that we can provide you with the best user experience possible. Cookie information is stored in your browser and performs functions such as recognising you when you return to our website and helping our team to understand which sections of the website you find most interesting and useful.
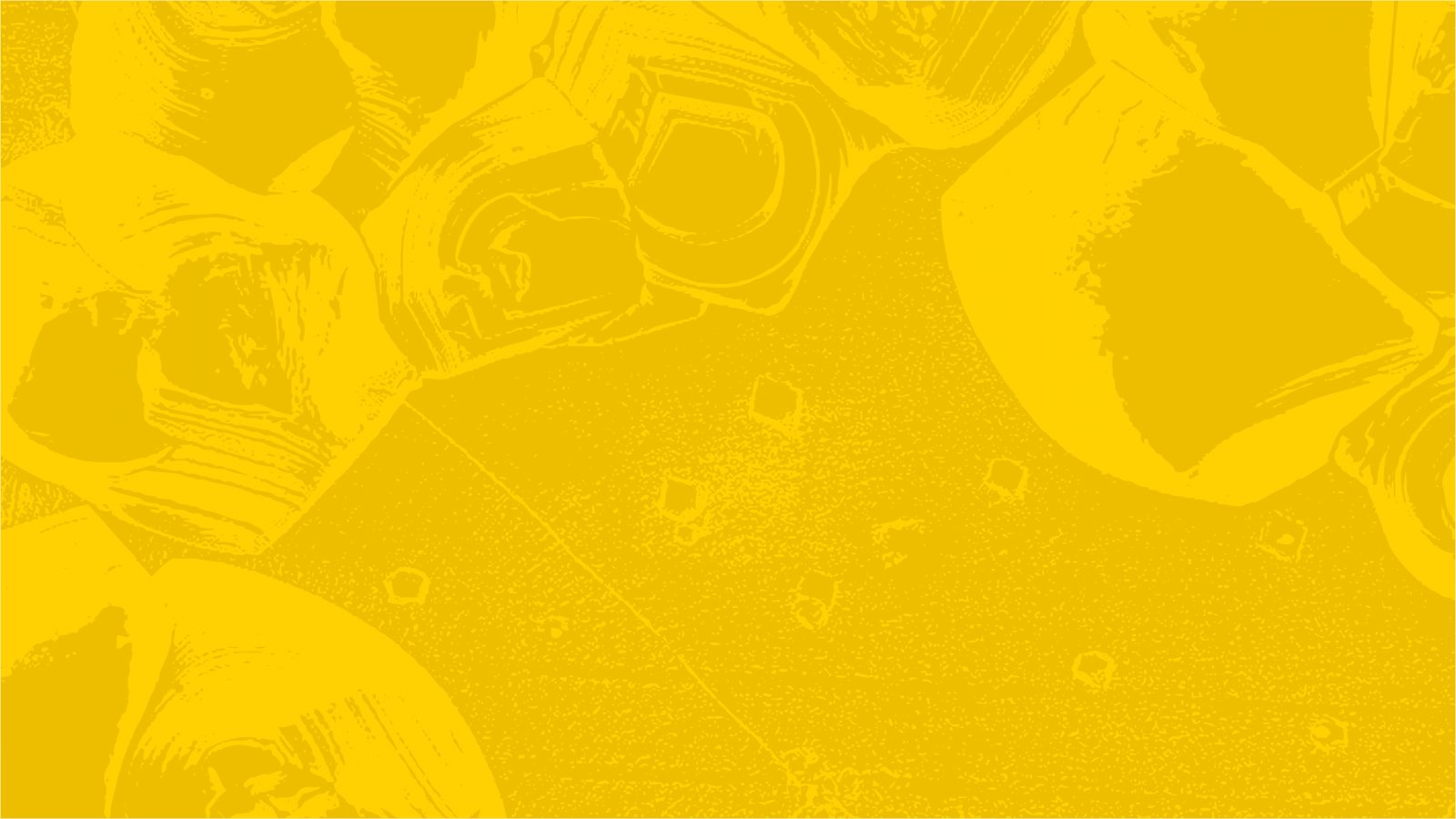
Single Step Printable Separator for high-throughput printed battery production
Case Study
Overview
The manufacture of Zinergy’s printed batteries involves multiple individual printing steps including the separator and electrolyte. These include cutting separator paper into required sizes, placing them on electrodes and printing a viscous liquid electrolyte over it. The objective of this project was to streamline the production process by developing a combined hydrogel system capable of performing the dual role of both the separator and electrolyte simultaneously. This integrated material system would have the potential to increase production efficiency and speed, reduce the carbon footprint and by offering a more robust electrolyte, minimise the risk of failure due to electrolyte leakage.
About the Project
Background
This project targets a very specific problem related to Zinergy’s roll-to-roll produced printable battery which is already on the market. A key area of development is known as “direct print”, where the battery cell is directly printed onto a circuit or label. This direct approach makes the process highly sensitive to failure-, as any battery malfunction impacts the entire device, resulting in increased costs.
A primary mode of failure is electrolyte leakage. This project aimed to address this issue by enhancing mechanical robustness through the development and integration of polymer gels, collaboratively formulated by the project partners. These polymer gels were specifically designed to complement Zinery’s existing electrolyte, effectively reducing the risk of failure. The successful implementation of these gels also presented the potential to remove the use of a separator, further simplifying the production process.
Achieving these outcomes would significantly improve reliability by reducing production failure rates from around 2% to below 0.5% which is required for widespread market adoption.
Project details and results
Throughout the 5 month collaboration, multiple UV-curable formulation variations were evaluated that yielded good battery performance results. Among approximately ten formulations tested, the formulation named “F05” was the most successful hydrogel system due to its excellent discharge performance. This formulation comprised of a blend of acrylic-type polymer and polyvinyl alcohol, selected for their favourable chemical properties and good compatibility with the battery electrolytes.
The key outcome of this project is the successful creation of a UV-curable electrolyte gel, offering rapid curing and sufficient mechanical stability to eliminate the need of a physical separator, whilst maintaining an acceptable electrochemical performance. Although the deposition method remains complex, the results justify continued investigations.
Expert guidance from Royce researchers proved instrumental in selecting the correct formulations. Successfully implementing these fundings would mean not only reduced waste, but also improved reliability and the applicability of the product in a wider range of applications such as food quality monitoring. Moreover, this work has provided all parties involved with new directions to explore and provides further scope for continuing collaboration.
This work has been excellent in proving that an initial seed idea is feasible in practice and potentially workable in production. It allows us to open a new direction of research to keep ahead of the competition in both reliability (reduced failure rate) and improved production efficiency (less production steps).
Pritesh Hiralal
CEO, Zinergy UK Ltd.
Collaborators
The work was completed with lead organisation Zinergy UK Ltd, working in collaboration with the University of Cambridge and Cambridge Smart Plastics Ltd.
The work was enabled due to a grant from the Henry Royce Institute’s Industrial Collaboration Programme.