Overview
Near Net Shape Manufacturing offers more efficient material usage, and can significantly reduce machining requirements to better meet national challenges in sustainability, recycling, and the circular economy. These processes can offer greater flexibility, previously inaccessible structures, and reduced costs for the next generation of complex components.
For Royce at the University of Sheffield, the capabilities enable UK industrial and academic communities to explore and expand metal technologies related to powder, wire, and melted ingot routes. This relates to leading and popular Additive Manufacturing techniques such as Selective Laser Melting and Electron Beam technologies.
Royce hosts equipment to deliver emerging processes such as Field Assisted Sintering Technology/Spark Plasma Sintering (FAST/SPS), as well as wire fed Directed Energy Deposition processes, and hybrid processes using post-process hot forging.
Additionally, the loop between feedstock and Near Net Shape components is closed within Royce – with a range of powder production facilities for use with alloys discovered/manufactured on equipment from other Technology Platforms.
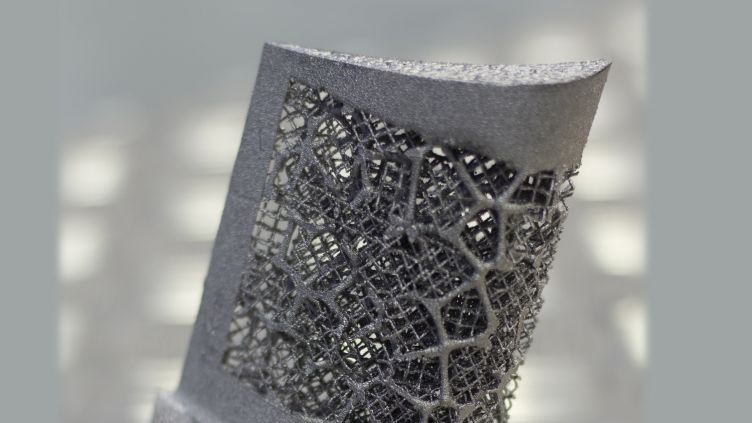
Capability
Royce at the University of Sheffield combines computational material design, high-throughput materials discovery, rapid scale-up, and material property screening, to deliver a step-change in the manner novel materials are developed for specific applications.
Our capabilities support the key technical challenge of innovating processes to efficiently fabricate and test material libraries, whilst simultaneously capturing sufficient information which can be shared with manufacturers to enable rapid deployment to occur.
Additive Manufacturing
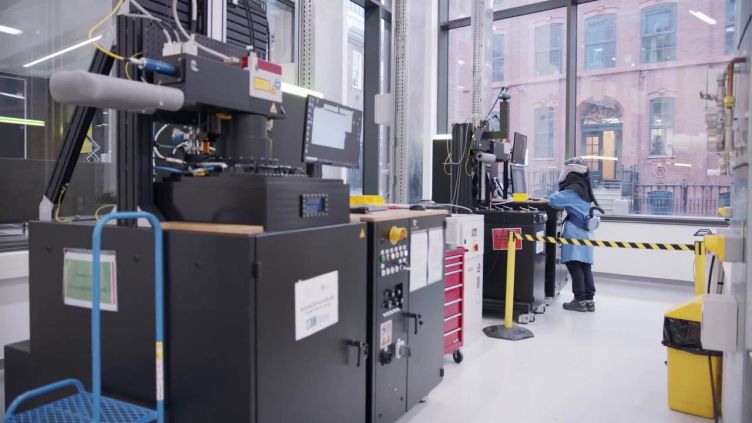
Powder Laser Bed Melting Suite
AconityLAB
AconityLAB uses a laser beam to selectively melt an area of metal powder based on a 3D model of a component, then repeating it layer by layer until the final geometry is obtained.
The machine is unique in that it is reconfigurable, both in terms of software and hardware. This enables the user to have complete freedom and control over the various processing parameters they can use, as well as the ability to change the machine components.
The ACONITYLAB is a truly modifiable lab system which can either be equipped with process monitoring tools, vacuum option or high-temperature preheating of up to 1200 ̊C. Its build volume is Ø 170mm x H 200mm.
The AconityMINI
The AconityMINI uses a laser beam to selectively melt an area of metal powder based on a 3D model of a component, then repeating it layer by layer until the final geometry is obtained.
The machine is unique in that it is reconfigurable, both in terms of software and hardware. This enables the user to have complete freedom and control over the various processing parameters they can use, as well as the ability to change the machine components.
The AconityMINI is an entry-level laboratory system with a build volume of Ø 140mmx H 200mm and is designed for efficient material research. It can be equipped with a preheating device, process monitoring or changed laser configuration.
The AconityLAB is a truly modifiable lab system which can either be equipped with process monitoring tools, vacuum option, or high-temperature preheating up to 1200°C. Its build volume is Ø 170mm x H 200mm.
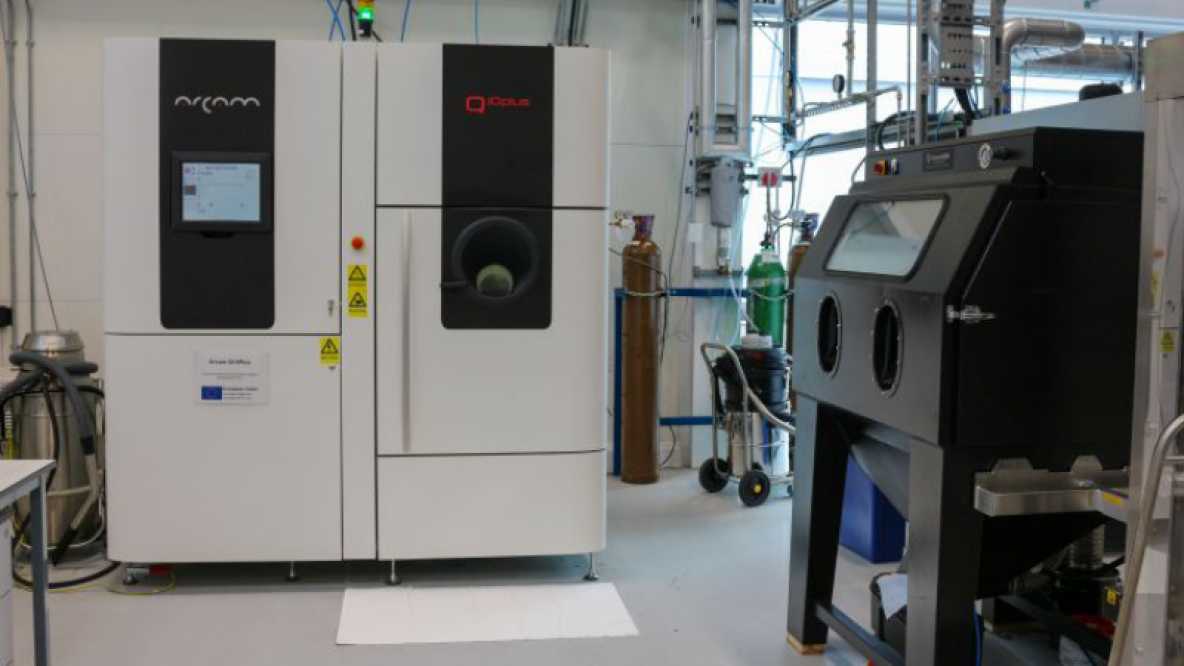
Electon Beam Melting
Arcam Q20Plus has the latest generation EB gun, which allows for higher productivity and improved resolution. It also includes Arcam LayerQam™, a camera-based monitoring system for inline part quality verification. The larger Q20plus is developed for easy powder handling and fast turnaround times. With an extended build volume (350 x 380mm (Ø/H), it is ideal for larger parts such as aerospace components.
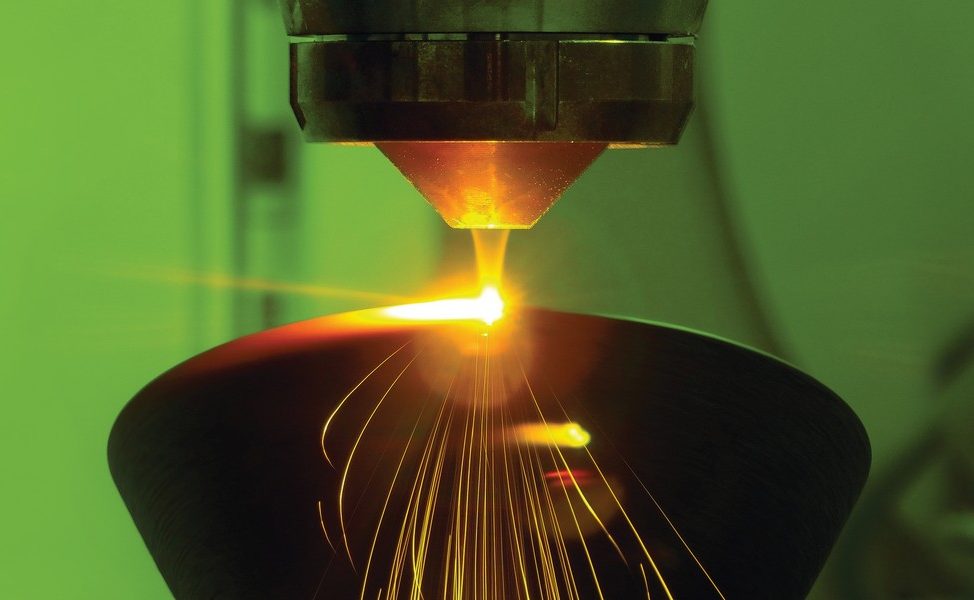
Directed Energy Deposition System
BeAM Magic 800 is a blown powder AM machine. Blown powder AM is commonly used by the aerospace sector to repair high-value components.
In this system, a deposition nozzle mounted on the Z-axis of a DED dedicated CNC (computer numerical control) machine is used. This allows continuous 5 axes of freedom to build/repair components layer by layer without the need for support structures.
The DED process involves directing metallic powder into a laser beam. The powder converges at the focal point of the laser, creating a melt pool which is laid down in a 5-axis configuration.
The machine’s capabilities include creating new alloys in situ so the properties of the deposited material can be changed during the build process. The build volume is 1200 x 800 x 800 mm.
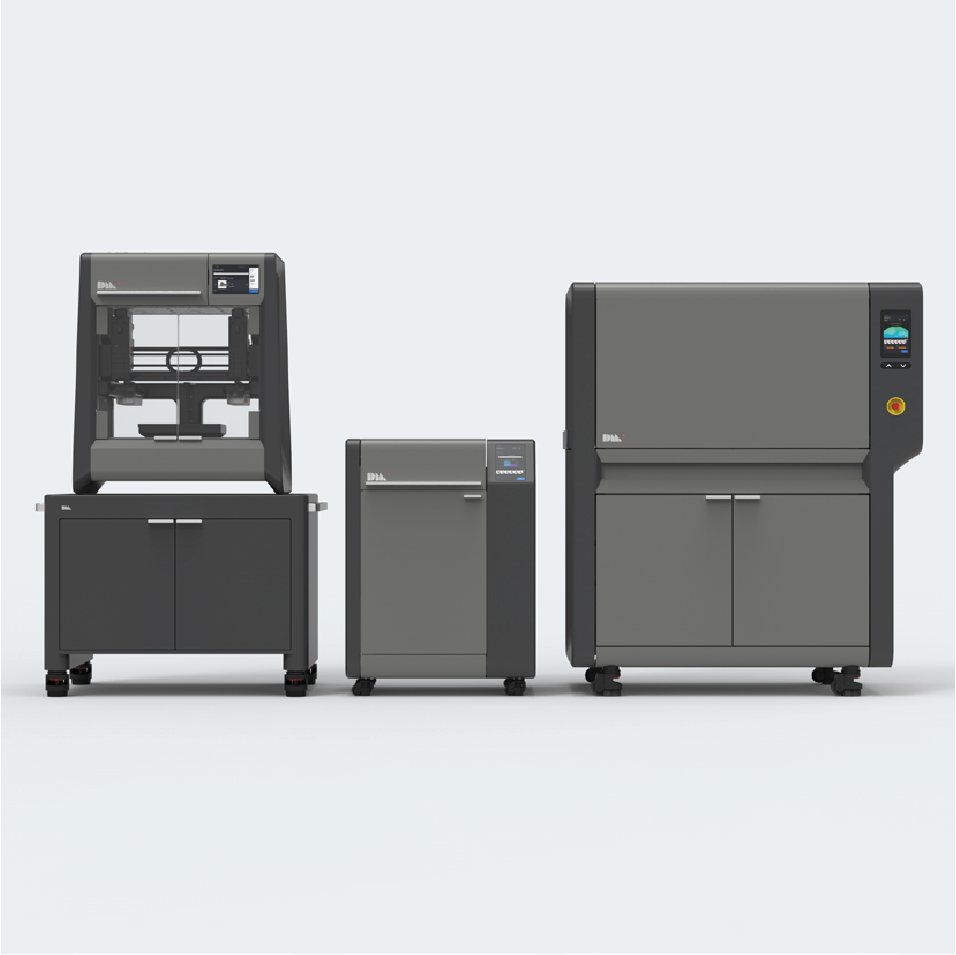
Bound Metal Deposition System
From CAD file, layer-by-layer, a green part is shaped by extruding bound metal rods [metal powder held together by wax and polymer binders] in a process called Bound Metal DepositionTM or Material Extrusion.
The green part is then immersed in proprietary rebind fluid, dissolving primary binder, and creating an open-pore channel structure throughout the part in preparation for sintering. As the part is heated to temperatures near melting, remaining binder is removed, and metal particles fuse together causing the part to densify.
This is an exciting, office-friendly metal 3D printer with great capabilities, and a scalable design for increased throughput.
Field Assisted Sintering Technology
FCT-HPD250/C & FCT-HPD25
Field Assisted Sintering Technology/Spark Plasma Sintering (FAST/SPS) uses a DC electric current to directly heat the mould and/or sample through Joule heating. This direct heating allows high heating rates and low processing cycle times to be achieved. Lower temperatures and mould pressures are also typical compared to conventional hot pressing and sintering techniques.
FAST/SPS offers new possibilities to manufacture numerous materials with potentially extraordinary characteristics. The Type HP D 250/C Furnace is ideal to investigate the scale-up of FAST/SPS for industrial applications.
Powder Production
ARCAST ATM DM50
Our inert gas atomiser incorporates induction melting capabilities to manufacture high quality, technically-advanced metal powders from titanium alloys and highly reactive, refractory metals. This atomiser gives the capability to produce bulk amounts of powder in a controlled atmosphere.
The size range depends on the material, pour temperature, and the interaction with the gas jet. The fine particles will be small and spherical, achieving sizes as small as a few microns.
TEKNA TEKSPHERO 15
Spheroidisation reduce internal porosity and provides high packing density while removing contamination and increasing purity. Removing excess oxygen from the material helps to improve mechanical properties in the completed part/component.
The TekSphero 15 enables us to meet the most demanding powder metallurgy applications including AM, metal injection moulding, and hot isostatic pressing. The powder developed at 15kW can easily be scaled up for production at higher power levels. It has a feed rate of up to 1kg/h and can produce powder sizes of up to 200μm.
The machine is suitable for processing refractory metals such as tantalum, tungsten, titanium, molybdenum, and niobium, as well as nickel-based superalloys.
Union Process - HD-01 and Union Process - S-1
The Attritor is ideal for formulating, quality control, and scale-up studies. Results are repeatable from one test grind to another for maximum credibility.
With the Attritor, users can choose wet or dry grinding, introduce inert grinding speed, overcome product contamination, change media size and type, get precise energy consumption, and information, all on one machine.
Hot & Cold Isostatic Pressing
AIP-AIP8-45H
In powder metallurgy, HIP allows us to compress a volume of metal powder at such high temperatures and pressures, that through a combination of deformation, creep, and diffusion, you actually create a product with an homogenous annealed microstructure (compact solid) with minimal or no impurities in the materials.
AIP-AIP3-12-60C
This research CIP is used to shape form powders into a green body, prior to sintering. This model allows the pressing of various shapes, including discs, bars, and tubes, and is therefore a near-net-shape process.