Overview
The Bioprinting Technology Platform is a national, open access facility that houses collaborative academic lab space and state-of-the-art equipment for production, testing and characterisation of 3D human tissue/organ analogues. Our objective is to support the Royce vision and accelerate commercial exploitation of bioprinting innovations (e.g. tissue/organ analogues) with potential socio-economic impact for the UK in key areas of research including human biology, medicine and drug discovery.
Bioprinting is an umbrella term commonly used to describe a group of additive manufacturing (AM) technologies (i.e. extrusion-based, material jetting, light and laser-assisted) capable of sculpting cells and biomaterials into 3D biological constructs that replicate the structural and functional organisation of human tissues and organs.
The BTP is fully equipped with state-of-the-art additive manufacturing (AM) and related techniques enabling the processing of both cellular and acellular inks into multiscale 3D constructs using multiple materials and cells (see equipment section below).
Recently, the BTP has been selected by the European Space Agency (ESA) to integrate a restricted consortium of ground-based facilities (5 in total) that researchers across Europe can access to carry out space-related bioprinting experiments. We also support multiple postgraduate research projects across the UoM and beyond, including PhD students from the CDT in Advanced Biomedical Materials.
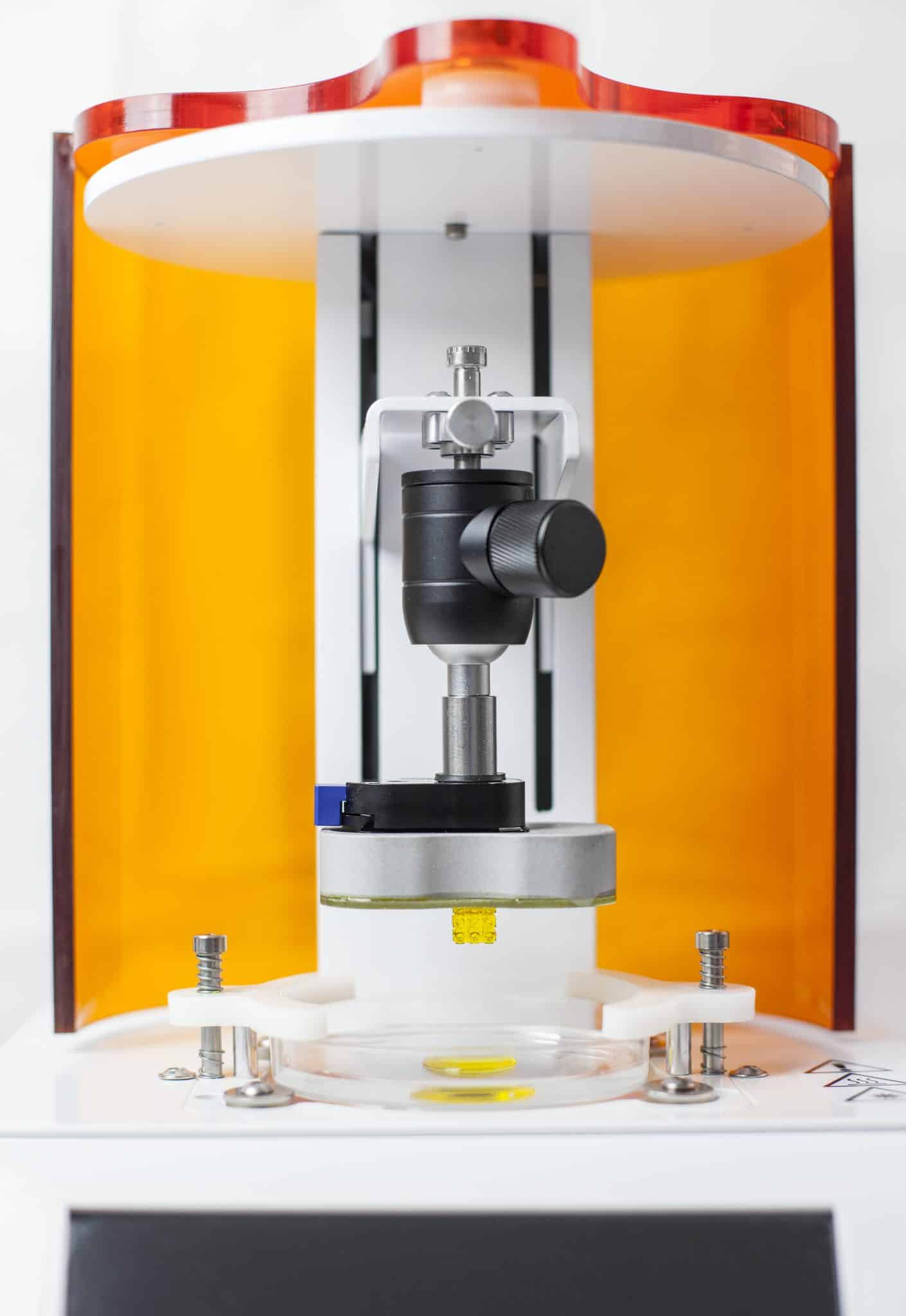
Technical Support
Jen Adcott is the primary Technical Specialist supporting the Bioprinting Technology Platform.
The platform is also supported by a dedicated team of Biomedical Technical Professionals within the Royce Hub Building.
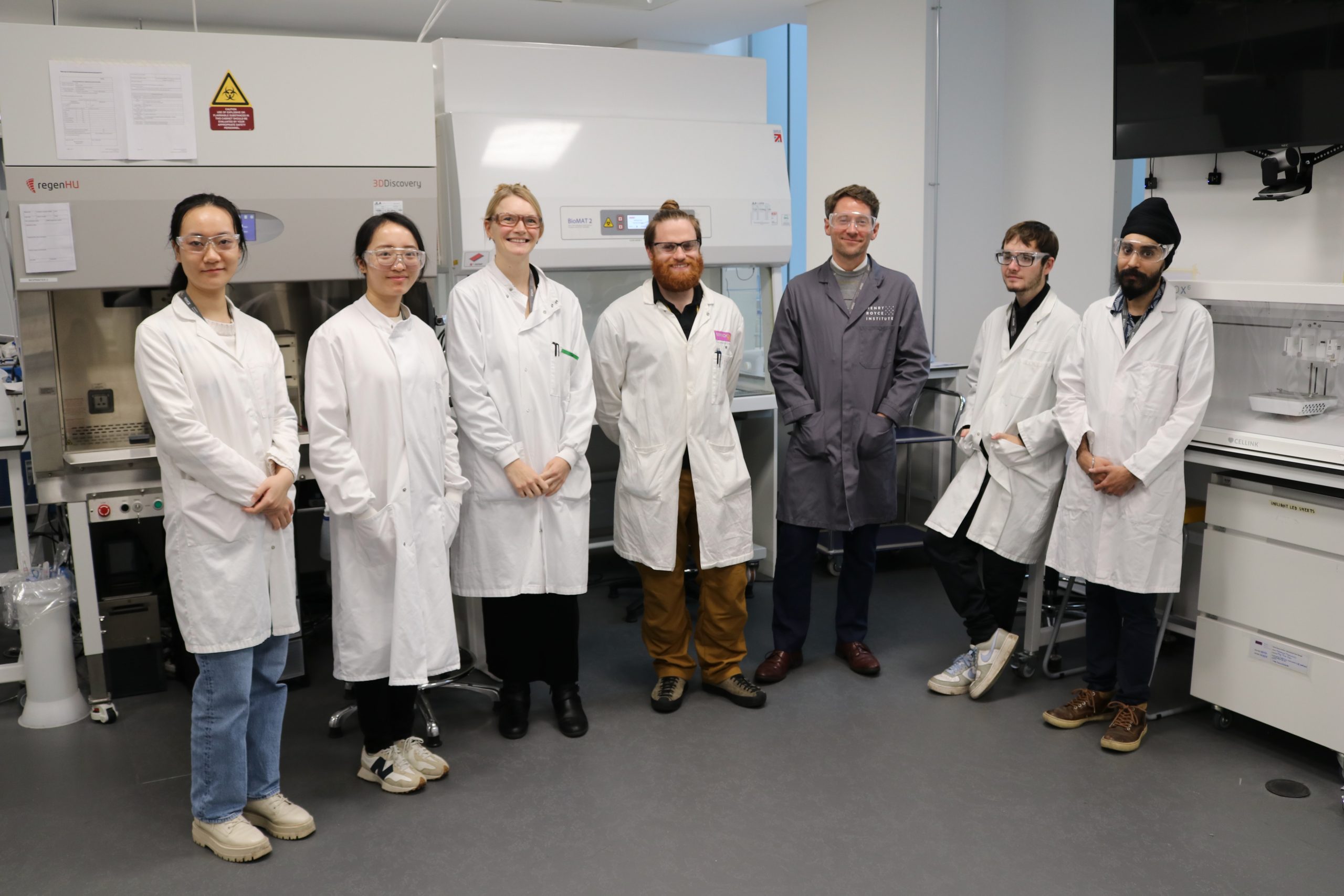
Capability
From light-assisted to extrusion or jetting processes we provide access to the most advanced bioprinting technology capable of processing a wide range of materials (i.e. photopolymers, thermoplastics, composites) at multiple scales (nanometre to micrometre) and production rates (0.1 – 100 mm3/min).
Depending on the targeted application, users can combine multiple techniques (e.g. extrusion and electrospinning), materials and cells in the same process to generate 3D constructs with gradients of function and structure. Importantly, the BTP is co-located with the cell culture, imaging, biomechanical and X-ray suites, allowing to streamline your project, improve efficiency and reduce risks of contamination.
3D Discovery Evolution Biosafety 1
This is a modular biofabrication platform allowing scientists to pattern cells, bio-molecules and shape a range of soft and stiff bioinks into desirable 3D constructs, mimicking the structural and functional organisation of natural environments. The platform is equipped with four different printing modules that can be operated independently or in combination to create multimaterial, multicellular and multiscale constructs:
Module 1 – non-heated, pressure assisted extrusion printhead for the deposition of cell-laden hydrogels
Module 2 – Screw-assisted extrusion printhead with temperature control for the deposition of acellular materials (e.g. thermoplastics, composites)
Module 3 – Direct Writing Melt Electrospinning (DWME) system for sub-micron layer-by-layer fabrication of polymeric constructs
Module 4 – Ultraviolet (UV) system enabling layer-by-layer photocuring of polymers. A high-speed CCD camera is also available for parameterisation and process control. The entire platform is enclosed by a Class 2 biosafety cabinet equipped with HEPA H14-Filtration and UV Lamp for decontamination, thus ensuring full sterility during the printing process. More technical specifications can be found here: https://www.royce.ac.uk/equipment-and-facilities/biofactory-tissue-printer/
3D Discovery Evolution Biosafety 2
Similar platform to the Evolution Biosafety 1 but equipped with different modules:
Module 1 and 2- Microvalve-based jetting printhead enabling the deposition of cellular suspensions or cell-laden hydrogels as either individual droplets or continuous stream
Module 3 – Direct Writing Melt Electrospinning (DWME) system for sub-micron layer by layer fabrication of polymeric constructs
Module 4 – Core-shell printhead enabling the fabrication of multi-layered constructs using up to two different materials and two different cell types
Module 5 – Ultraviolet system enabling layer-by-layer photocuring of polymers. A high-speed CCD camera is also available for parameterisation and process control. The entire platform is enclosed by a Class 2 biosafety cabinet equipped with HEPA H14-Filtration and UV Lamp for decontamination, thus ensuring full sterility during the printing process. More technical specifications can be found here: https://www.royce.ac.uk/equipment-and-facilities/3d-discovery-electrospinning/
Nanoscribe Photonic Professional GT2
This is one the most advanced mask-less lithographic systems on the market enabling the two-photon polymerization (2PP) of 3D constructs (with or without cells) with sub-micron resolution and feature sizes down to 200 nm. More detailed specifications can be found here: https://www.nanoscribe.com/en/products/photonic-professional-gt2#tab-17297 and here: https://www.royce.ac.uk/equipment-and-facilities/stereolithography-2photon-stereolithography/
sPRO 60 HD-HS 3D Printer
Selective laser sintering system with unique flexibility in terms of printing parameters enabling to process the widest range of biomedical materials available in the market. In particular, the 70 W / CO2 laser allows for the production of highly accurate and reproducible 3D constructs using low melting temperature and FDA approved polymers such as Polycaprolactone (PCL) among others. More technical details can be found here: http://infocenter.3dsystems.com/product-library/sls/spro-60 and here: https://www.royce.ac.uk/equipment-and-facilities/selective-laser-sintering-biomedical-polymers/
Lumen X
This printer leverages DLP and visible light to create high resolution, high throughput and high-fidelity 3D constructs enhancing applications in cell-laden hydrogels or microfluidics. Equipped with 65×35 mm heated Platform (up to 37°C), light source wavelength of 405 nm and intensity range of 10 – 30 mW/cm2, this is an ideal system for development, testing and optimization of photopolymers for bioprinting. More details can be found here: https://www.cellink.com/bioprinting/lumen-x/
BIOX 6
This printer is equipped with 6 modular intelligent printheads enabling the fabrication of multi-material, multiple cell line and multiscale constructs using micro-extrusion, light-assisted or material-jetting technology, independently or in combination. The system is fully enclosed in a clean chamber equipped with dual HEPA filters for sterile printing. The 4 UV modules (365, 405, 485 and 520 nm) plus the visible green-light tool head (520nm) allow for the automated crosslinking of photopolymers in a layer-by-layer fashion. Temperature controlled printheads and building platform ensure an optimal processing of cells and other biomolecules.