Overview
The Royce Thermomechanical Processing Technology Platform combines advanced capabilities in forging and hot rolling with cold rolling and sheet metal processing, enabling the development of the next generation of high-value added wrought metal products and processes. The facility also provides small-scale simulation and characterisation equipment to give users integrated analysis and modelling capability for materials processed within the platform.
The unique system of equipment that sits within the Technology Platform permits processing at a scale that is industrially relevant but also small enough to handle in a laboratory environment, meaning the majority of the capabilities within the platform can work samples with a volume of approximately 1 litre.
The platform sits within the Advanced Metals Processing (AMP) research theme at Royce and operates in conjunction with other AMP Technology Platforms: Materials Discovery and Prototyping, Near Net-Shape Manufacturing and High Integrity Forging to create an interlinked research pathway for users. The capabilities provided through the Thermomechanical Processing Platform and other AMP facilities also support innovation across many Royce research themes including Materials Systems for Demanding Environments and Nuclear Materials.
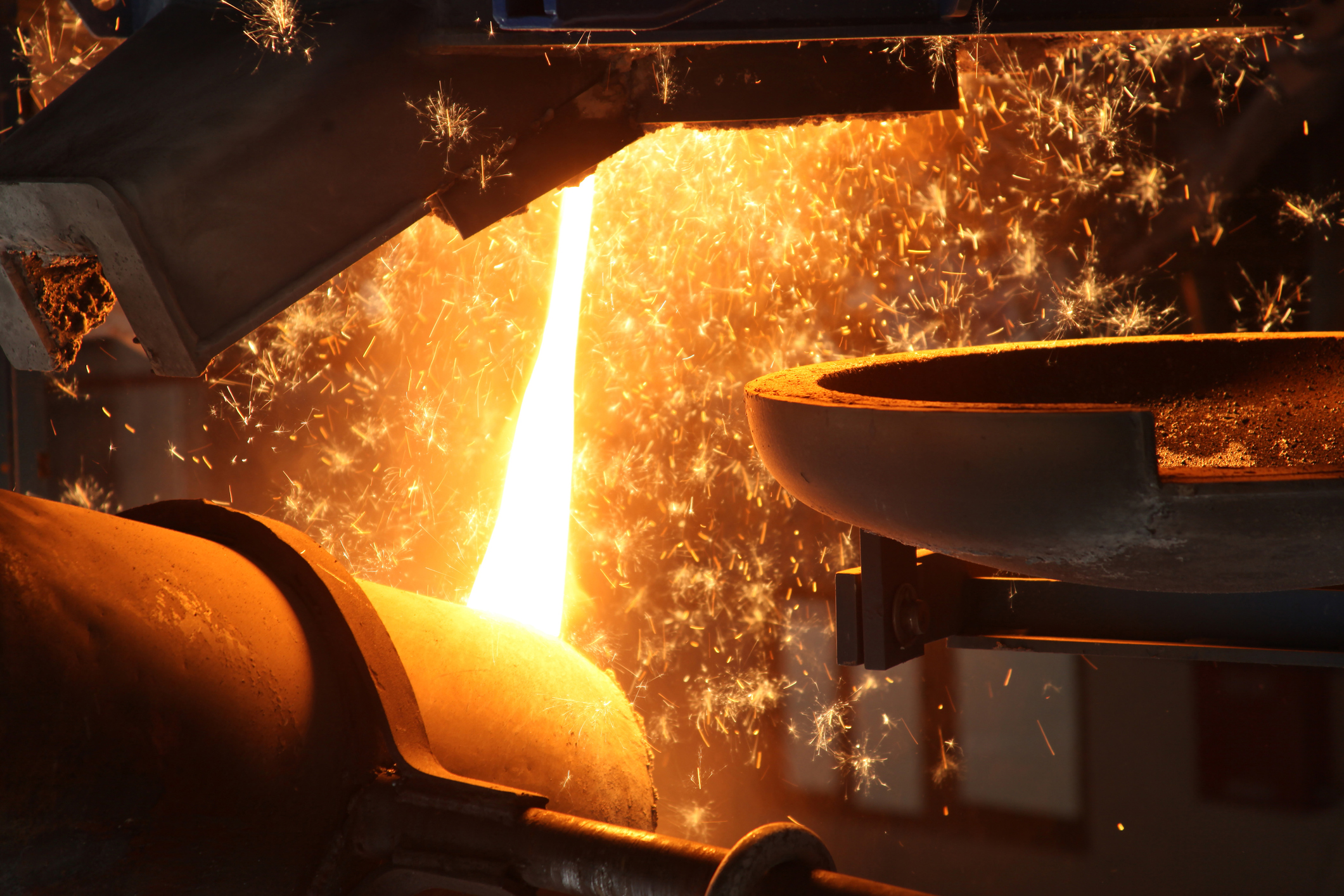
Capability
The Royce Thermomechanical Processing platform sits on the ground floor of the Royce Hub Building at the University of Manchester, and contains a broad spectrum of equipment for experimental projects using metallic materials.
Hot Rolling, Forging and Extrusion
An advanced electric forging hammer (Schuler) and hot rolling mill (Fenn) allow for the breakdown of the 1-litre ingots produced by the AMP Materials Discovery and Prototyping capability, as well as advanced thermomechanical processing research (e.g., FAST forge process). While using our continuous extrusion capability (BWE) we can transform metal powder, swarf and rod into long products and wire.
Cold Rolling and Sheet Metal Forming
A Fenn cold rolling mill capable of operating in 2-high or 4-high configuration allows the processing of materials up to 300mm wide down to thicknesses of 500µm (2-high) and <200µm (4-high). With a separating force of 180MT (396,832 lbs) we are able to process a wide range of alloys including aluminium, steel, magnesium, titanium and nickel.
Sheet produced internally or supplied by collaborators can be investigated using the Interlaken ServoPress SP225 fitted with GOM 3D digital image correlation equipment. The six different punches allow a breadth of forming investigations to be conducted on a given material. Custom tooling plates allow for research to be undertaken on scaled versions of production pieces to aid in product development during stamping operations.
Small Scale Simulation and Characterisation
Using the TA Instruments DIL805 A/D/T it is possible to conduct high-precision simulations of complex thermomechanical processing involving tension, compression and quenching using a range of heating/cooling rates at temperatures up to 1500°C. Alongside this is the Gleeble 3800-GTC fitted with both the pocket jaw MCU (heat cycling, tension and compression testing) and Hydrawedge (rolling, forging and plane strain simulations). Thermodynamic characterisation is supported through a Netzsch 404 F1 Pegasus high temperature DSC capable of testing up to 1650°C.
Mechanical Testing
To supplement the thermomechanical processing, we have six mechanical testing frames to cover a range of testing on materials that have been processed within Royce or at external partners. The capabilities include:
- High-speed load frame (20m/s maximum speed) capable of testing in tension or compression accompanied by high-speed digital image correlation to monitor strain evolution during testing.
- Instron 8862 low cycle fatigue frame fitted with Severn Thermal Solutions Vacuum Furnace to test samples under vacuum or inert atmosphere up to 1000°C.
- Instron 8862 low cycle fatigue frame capable of testing up to 1000°C or fitted with ESPEC humidity chamber for controlled humidity testing up to 300°C.
- Tension-torsion load frame allowing for multi-axial testing of samples from room temperature up to 1200°C.
- Two Zwick Amsler 50 Vibrophores with a range of fixtures to allow fatigue testing of wide range of specimens.