Overview
The Fuels and Irradiated Materials Analysis platform is a national, open-access facility for academic and industry collaborators via Royce or National Nuclear User Facility (NNUF) access schemes. It houses academic laboratory space and state-of-the-art active equipment for the manufacture, characterisation, testing and post-irradiation characterisation of α, β and γ active nuclear materials to support current nuclear power generation, and the advanced nuclear and nuclear fusion materials research areas. This mainly supports the Royce Research Area of Nuclear Materials but also supports Materials for Extreme and Demanding Environments (MS4DE) and imagining and characterisation.
The nuclear fuel technology facilities housed within the Nuclear Fuel Centre of Excellence (NFCE) and the Henry Royce Institute at the University of Manchester include various experimental capabilities to synthesise, fabricate and characterise representative fuel materials. A suite of inert atmosphere gloveboxes, housing a variety of equipment, provide the capability to handle and process uranium- and thorium-bearing metals, ceramics and intermetallics. The research team at Royce has developed capabilities to synthesise and fabricate representative fuel forms from a variety of uranic materials, including metal alloys, nitrides, silicides, carbides, borides and oxides. A range of experimental techniques have been developed over the past decade to allow thermophysical analysis, material characterisation and various forms of microscopy to be utilised on uranium-bearing materials.
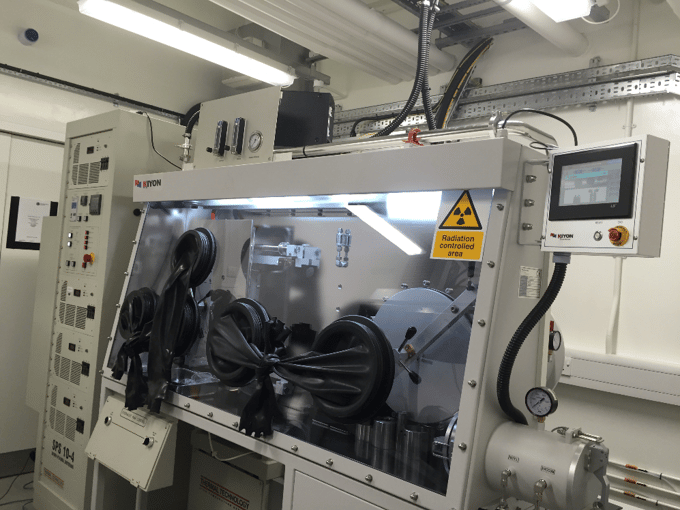
Capability
The irradiated materials facilities housed within the Henry Royce Institute at the University of Manchester include various experimental capabilities to investigate irradiated materials high-temperature nuclear systems and materials degradation in these environments. The research team has developed a dedicated radioactive laboratory to prepare, characterise and test irradiated samples including graphite and Zr alloys. Equipment capabilities include sample machining, preparation, radiometric and radiological fingerprint characterisation (α, β and γ), microstructural characterisation (2 and 3D) including spectroscopic & crystallographic, and in-situ testing (both mechanical and environmental, and chemical and physical treatments with on-line spectroscopic evaluation). Further equipment specifications are given below.
Manufacture
Arc melter (inert atmosphere glovebox)
Vacuum/inert atmosphere graphite furnace (2200°C)
Spark plasma sintering furnace (Glovebox coupled, 2700°C)
H2 /N2 /Ar tube furnace (1800°C)
H2 /N2 /Ar tube furnace (inter atmosphere glovebox, 1400°C)
Flash sintering Furnace (1600°C)
Mixer/ball/rotary milling
Chemical vapour deposition furnace
Hot isostatic press (2000°C, 300 MPa)
Characterisation and Testing
Thermogravimetric analysis (1600°C) – including water vapour
Differential scanning calorimetry (1600°C) – including water vapour
Dilatometry (1200°C)
Laser Flash Analysis (1200°C)
Dynamic mechanical analysis (600°C)
Laser confocal microscopy
Raman microscopy
Atomic force microscopy
X-ray diffraction crystallography
X-ray computer tomography
Metallographic sample preparation (inert atmosphere glovebox)
He-pycnometry
Particle size analysis – laser diffraction
Surface area analysis – BET
Electron Microscopy
NovaNano scanning electron microscopy (SEM) equipped with:
- A Field Emission Gun (FEG) electron source
- Electron Backscatter Diffraction Analysis (EBSD) and Energy Dispersive X-Ray (EDX)
- Nano-indentation
- High temperature air/steam injection capability to examine high temperature corrosion and oxidation on the micron scale
Helios G5 focused ion beam (FIB)/SEM equipped with:
- A Field Emission Gun (FEG) electron source
- Secondary Electron (SE), Backscattered-Electron (BSE), Circular Backscatter Detector (CBS), scanning transmission electron microscope (STEM) detector – resolution of 0.7 nm
- Oxford instruments Ultimax EDS 170 mm2 detector, Oxford instruments Symmetry fast CMOS EBSD camera
- AutoTEM lamella preparation, Slice and view software for 3-D electron image, EDS or EBSD capture
- Alpha active loader with coupling to MBraun glovebox to permit fully contained workflow for alpha active nuclides
Talos 200i scanning transmission electron microscope (S/TEM) equipped with:
- FEG electron source with probe size down to 1 nm
- Bright-field (BF), Annular dark-field (ADF), High Angle Annular Dark Field (HAADF) detectors
- Dual Bruker EDS systems with energy resolution of 129 eV
- Gatan Continuum EELS camera for spectroscopy of EFTEM image acquisition, energy resolution of 0.9 eV
- Range of holders, including low background EDS, Cryogenic and Vacuum/ inert transfer holders to go from FIB glovebox to S/TEM without breaking of containment/exposure of the sample to air
Active Sample Preparation
A water jet cutter
TEM mill and associated ancillaries
Spark erosion machine
Optical microscopes
Supplementary facilities including ovens, balances
Twin jet electropolishers for TEM sample preparation
Various cutters, Diamond saws and active lathe
High Temperature Testing
2 x 1000°C thermal treatment rigs with online Mass Spec analysis of evolved gases and 3H/14C analysis
Instron load frame and 30 KN load clee coupled to a 2000 °C Creep furnace rig complete with gas analysis and 3D micro DIC
High (3000 °C) sintering furnace
Beta high pressure (200 bar) high temperature (360 °C) Autoclave, 1.6 l vessel Physical characterisation
PoreMaster 60GT pore volume measurement
Porometer 3G pore size distribution
Resonance frequency and damping analyser
Olympus panametric Ultrasonic testing
Pheonix TE66 dynamic mechanical analyser
Micromeritic Tristar II surface area analyser
Radiometric Characterisation
Packard Tri-Carb 3100TR
Canberra NAIS-2×2
Canberra HPGe detector
Autoradiography