A History of Metals
Select a heading below to learn more about the history of metals. Each link corresponds to a section of the Henry Royce Institute exhibition Metals: Pioneering Materials and provides more insight and detail into the period.
Why Are Metals Special? Magical Materials
The magic of metals was first revealed by our ancestors, who discovered native metals in mineral deposits or in ores. The colours and shapes of native metals would change with time, leading to the belief that they contained mystical properties. Native copper, for example, is a red-brown metal that changes into a green-blue colour when exposed to the environment. Although this process is now known as oxidation, in the eyes of our ancestors this might have been seen as magical!
Metals also seemed magical in other ways. Humans have used fire for warmth, light, protection and to cook for millennia. By adding certain coloured rocks to a fireside, it was possible to create a shiny fluid with the heat, that formed a new shiny solid when cooled. This accidental melting of native metals could be compared to the later development of alchemy, whereby practitioners attempted to turn common materials into rarer ones such as gold.
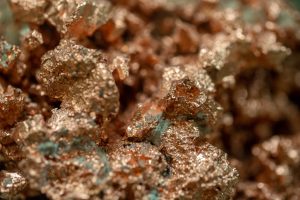
Native Copper Seen in its Pure Form
Due to their shiny appearance, metals such as native silver and gold were originally used for decorative purposes. Even today, some metals are still used as a display of wealth and as symbols of status. The earliest evidence of native metals used for decorative purposes is recorded in the archaeological record from around 10,000 BC (about 12,000 years ago). From around 8,000 BC (about 10,000 years ago) native metals such as copper, silver or gold started to be extracted by applying heat to their ores, a process that we now call smelting.
Metals were also durable materials. Items made of metal would last longer than items made from other materials like wood and stone. However, the skill of metal production remained rather difficult to master and for thousands of years metal goods would have been luxury items and mysterious objects to many.
The Power of Transforming Materials: The Age of Metals
As humanity understood more about how to extract metals from mineral sources, their transformation began to drive and influence technological advancement through the ages. The study and practice of working with metals, known as metallurgy, can be traced by historians and archaeologists to identify advances in the use of these materials across different civilisations.
The classification system historians use to refer to these advances in prehistoric world are commonly known as the Metals Ages, and can be divided into three periods: the Copper Age, Bronze Age and Iron Age.
Not all civilisations, however, followed the same progression from copper to bronze to iron. In areas rich in iron, but poor in copper, cultures often began working with iron earlier than other cultures, but with limited earlier development using copper or bronze.
Regardless of their chronologies, the Metal Ages was the period when metals superseded stone as a material of choice for many applications, bringing with it the rise of new ideas, trades, migrations, and societies.
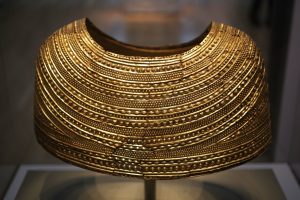
The Mold Gold Cape is a ceremonial garment produced from a single ingot of gold. The cape was produced in the British Bronze Age between 1900-1600 BC (‘Mold Cape’ image by GENI – Licensed under CC BY-SA 3.0)
The Three Periods
The Copper Age
The Copper Age is defined by the abundance and nearly exclusive use of copper. Although the earliest evidence of copper manipulation from native ores or for decorative purposes predates the beginning of the Copper Age, conventionally, the Copper Age starts around 5,000 BC (about 7,000 years ago) and ended around 3,500 BC (about 5,500 years ago) depending on the region.
The Bronze Age
The Bronze Age is a period characterised by the widespread use of bronze. Conventionally, it starts around 3,500 BC (about 5,500 years ago) and ends around 1,200 BC (around 3,200 years ago) depending on the region. Bronze is a metal alloy1 mostly composed of copper and tin, alongside small amounts of some other metals that are often added.
The Iron Age
The Iron Age, resulting from the development of iron technology, is thought to have started around 1,200 BC (about 3,200 years ago) and it ended in different periods depending on the region.
From Romans to the industrial revolution: a story of iron and steel
Progress in manufacturing techniques for iron through the Middle Ages (500 -1500 AD) led to this metal becoming one of the most important materials of the era, replacing the use of materials commonly used through the Metal Ages and expanding the applications of metals used in society.
For over two thousand years (after its earliest recorded use during the Metals Ages), the most common type of iron available was called wrought iron. Wrought iron is an iron alloy with a very low content of carbon (less than 0.08%). Initially, this type of iron was created by heating and then shaping the metal with a hammer when it was softer to expel the impurities in a long process made by skilled blacksmiths. This is the reason why it was called ‘wrought’ which means ‘worked’. As early as 200 BC (about 2,200 years ago) in Asia, wrought iron started to be produced at scale in forges and commercial production was then introduced to Europe in the late medieval period. Although wrought iron is a highly malleable and ductile1 metal, its production process was long and complex. As a result, wrought iron was initially used in small quantities and later mostly used to make weapons, armours, and then later to create the first railway tracks.
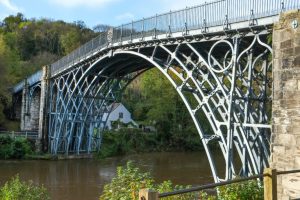
Ironbridge, the world’s first iron bridge was erected over the River Severn in Shropshire in 1779
Another type of iron, cast iron, appeared in ancient times in China (as early as 500 BC – about 2,500 years ago) but did not become widespread in Europe until the late medieval period. From the 1300s, the invention of the blast furnace and casting process led to iron being produced on a much larger scale. The high temperature of a blast furnace made it possible to completely reduce iron ore, and then cast it into moulds to create cheap and standardised items. These new manufacturing techniques led to cast iron being used in cannon balls and then as a structural material in bridges, buildings and railways. Cast iron is, however, an alloy of iron which contains a relatively high amount of carbon (over 2%) making it a brittle material which is unsuitable for items subject to powerful impacts and regular stress. This is the reason why a cast iron railway bridge collapsed under its own weight on the Chester and Holyhead Railway in the Dee Bridge disaster of 1847.
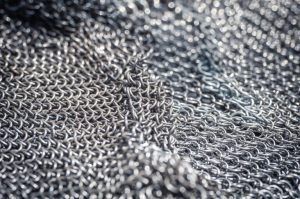
Chain mail is a type of armour that was commonly worn in the Middle Ages, consisting of small iron rings linked together to form a protective mesh
In search of a tougher metal, humans created steel. Steel is another iron alloy that contains a relatively low amount of carbon (less than 1.5%)5. Steel has existed since ancient times, made either deliberately or accidentally, but it remained very hard to produce for many centuries. The earliest evidence for steel manufacture can be traced back as early as 400 BC (about 2,400 years ago) in Asia. The specialist knowledge needed to make steel did not become widespread and steel manufacturing was limited to a small number of sites.
During the European “Age of Enlightenment” in the 1700s, a new manufacturing method called the Huntsman process (named after its inventor), made it possible to produce a stronger and more resistant metal: crucible steel. This was produced by using a fired furnace capable of reaching temperatures over 1600°C, far hotter than any blacksmith’s forge.
By the 1800s another new manufacturing approach – the Bessemer process – allowed the first mass production of steel at a much lower cost. This process removed the excess carbon and impurities by blowing hot air through the molten iron in a controlled manner within the blast furnace. This led to the industrialisation of steel and its use in buildings, ships, and machinery.
Due to its enhanced properties and low cost, steel is now one of the most used metals in the world.
Modern metals: Aluminium
Aluminium is one of the most abundant elements on the planet, making up around 8% of the Earth’s crust. Although it is one of the most widely used metals in the world, it took centuries for scientists to isolate the naturally occurring aluminium compounds found in rocks, clay and soil.
This changed in the late 1820s when the first lumps of aluminium in the form we know it now were produced by heating potassium amalgam with aluminium. Its production, however, was still far too expensive and was used only as a luxury metal. With a cost higher than gold, members of high society
would display aluminium items to impress their guests.
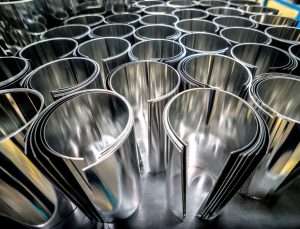
Aluminium sheets are used to manufacture a vast range of products we use each day
Commercial production of aluminium at scale was only made possible by the discovery of the Hall-Héroult process in 1886. This uses an electrical current to cause a chemical reaction which releases aluminium from its ore. With the widespread adoption of electricity during the 1900s, aluminium became cheaper to extract and this previously exclusive luxury metal became the most widely used non-ferrous1 metal in the world.
The invention of the microscope helped us understand the properties of this ‘new’ metal. It was observed to be lightweight, strong, malleable, conductive2, and resistant to corrosion. These properties make it ideal for a wide range of applications from cookware to food packaging, electronic goods, vehicles, aircraft and even spaceships. Aluminium was the lightweight, corrosion resistant metal that many important technologies had been waiting for!
A new microworld: revealing the magic
Light microscopes, as we know them today, were developed between the 1500s and 1800s – born as a product of human curiosity and the desire to understand the world around us at a deeper level.
Microscopes enabled scientists to understand the properties of different materials at the microscopic level. For the first time, microscopes showed us that metals are made of tiny crystals, called ‘grains’. The shapes and structures of these grains would change depending on the composition and the process by which they had been made.
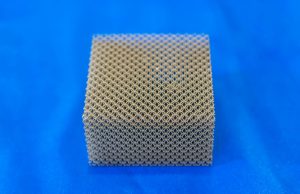
The crystal structures of metals are formed by individual rows of atoms arranged into 3D structures containing long-range repeating patterns
The invention of the electron microscope in the 1930s further improved our understanding of materials, allowing us to observe them at higher magnifications than under light microscopes. More recently, electron microscopes have allowed us to see the individual rows of atoms in metals, and how they arrange into 3D structures that have a long-range repeating pattern in space – i.e. crystal structures. The microscopic crystal structures of different metals could finally be seen and analysed by humans.
This microscopic understanding led us to design new metals and alloys with specific properties that suit the needs of the modern world. For thousands of years, humanity used only a few major metals – in the last fifty years, thousands of different metals and alloys have been discovered for us to use for different applications.
Modern-day magic: superalloys and demanding conditions
Today, metals are being used for a myriad of new applications that were not thought to be possible a century ago. The need for new components for use in extreme environments such as jet engines and nuclear reactors has led to the creation of superalloys.
Superalloys are metal alloys which are resistant to extreme temperatures and often exceed the performance of regular alloys in characteristics such as mechanical strength and corrosion resistance. These high-performance materials are adopted primarily in specialised applications such as in aerospace and marine turbine engines or heat exchangers for nuclear reactor systems. Superalloys are typically used in the hottest section of rocket engines where temperatures exceed 1200°C!
Superalloy manufacturing is often technically complicated and expensive, but the performance of these materials in engines and other energy systems often provides sustainable and long-term financial benefit at their point of use. Nickel-based superalloys, for example, combine exceptional strength with high corrosion resistance, making them more efficient in chemical processing and aerospace applications than other alloys.
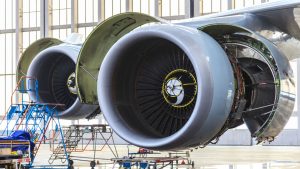
Research into superalloys means we can now use metals in extremely demanding environments such as in a jet engine
Another distinct range of technically complex alloys are widely used as ‘biomaterials’. Biomaterials are materials that we use to help replace and repair parts of the human body. A very common example of this is in hip replacements, where metallic parts have been used for decades to replace the top of the femur bone. Originally, stainless steel materials were used in such applications, but these were found to degrade inside the body (which is a demanding environment!). Today, titanium alloys are the preferred choice owing to their improved corrosion resistance and better match to the mechanical properties of bone. Titanium parts have been further improved by specialised processing (including 3D printing for bespoke personalised parts) and advanced coatings to enable better attachment with the rest of the femur. Moving forwards, biomaterials researchers are focussing on using materials to help the body repair itself, rather than using them to replace parts. ‘Resorbable’ biomaterials, which are naturally broken down by the body after they have performed their task, are a hot topic at present, and an area where alloys are likely to play a key role.
Although many of these technically complex metal alloys and superalloys are not commonly known, they are critical to the functioning of the most widespread modern technologies. Metals are always around us, and you might be surprised by the prevalence of materials science all around you!
About the Objects
The exhibition features a number of metal objects commissioned by Royce to give attendees a hands-on look at how metals were used in medieval armour. Select one of the links below to learn more about the objects.
Kettle Hat Helmet
A kettle hat, sometimes known as a war hat, was a type of helmet popular throughout the medieval period. This helmet design took its name from its similarity to a metal cooking pot. The kettle hat was widely used by infantry in the Hundred Years War (1337 – 1453), and was so efficient in protecting wearers from projectiles that an adapted design, the Broadie helmet, was reintroduced in both World War 1 and 2.
Kettle hat helmets were typically made from iron or steel. Their inexpensive and simple design meant they could be produced rapidly and did not require a great amount of skill to manufacture relative to other helmet types.
The wide brim of the helm provided enhanced protection against blows from above, such as cavalry swords and projectiles and held advantages over other types of helmet because it did not interfere with the wearer’s vision, hearing or breathing.
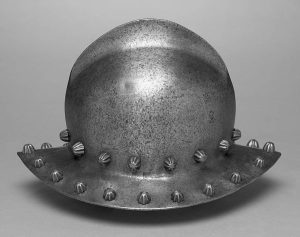
A kettle hat helmet, featured in the Metals: Pioneering Materials Exhibition
About the object
The object displayed in the Metals: Pioneering Materials exhibition is a replica kettle hat commissioned for the exhibit.
The helmet displayed is made from steel. Steel is a high-density alloy (from 7750 kg/m3 to 8050 kg/m3). This is typically 2.5 times denser than aluminium, making it much heavier. Steel is a desirable material to use for helmets because it is strong and less likely to warp, deform or bend under weight, force or heat.
Vambraces
Vambraces are a type of forearm guard that makes up part of a suit of plate armour. Vambraces were usually combined with gauntlets or elbow defences to provide the wearer with enhanced protection.
This piece of armour was conventionally produced from a range of materials including iron, steel, brass and even leather. Vambraces gained popularity in the medieval period as the use of large, heavy, shields became less favourable. Vambraces did not interfere with the wearer’s mobility and could be shaped to fit the user’s profile, allowing for a lighter burden during combat.
The objects displayed in the Metals: Pioneering Materials exhibition are replica vambraces commissioned for the exhibit.
Although all three forearm guards have the same shape and size, each has a very different weight. This is because they are made from different metals.
The weight of the different objects depends on the density of atoms in the metals they are made from. Density is a measure of how heavy an object is for a given size. With the exception of aluminium, most conventional metals are very dense. This is because they are made from heavy atoms which are packed together densely arranged ‘crystal’ structures.
You can feel these different densities of metals if you wear the three vambraces.
Vambrace 1 is made from steel. Steel is a high-density alloy from 7750 kg/m3 to 8050 kg/m3). This is typically 2.5 times denser than aluminium, making it much heavier. That is why a steel vambrace is strong and less likely to warp, deform or bend under weight, force or heat.
Vambrace 2 is made from aluminium. In its pure form, aluminium has a very low density (about 2,710kg/m3), which means it is a lightweight metal. For this reason, aluminium is the preferred metal choice for many applications such as vehicles, aircrafts, or spaceships! Aluminium is also a relatively soft metal, but when combined with another metal (in an alloyed form), it hardens and strengthens. Aluminium is also resistant to corrosion because it forms a thin layer of its oxide on the surface of the metal. This keeps air and water from getting into the metal which causes corrosion.
Vambrace 3 is made from brass, which has been used here as a substitute for copper considering the high commercial value of copper. Brass is an alloy composed of copper and zinc with a high density (from 8400 to 8700 kg/m3).